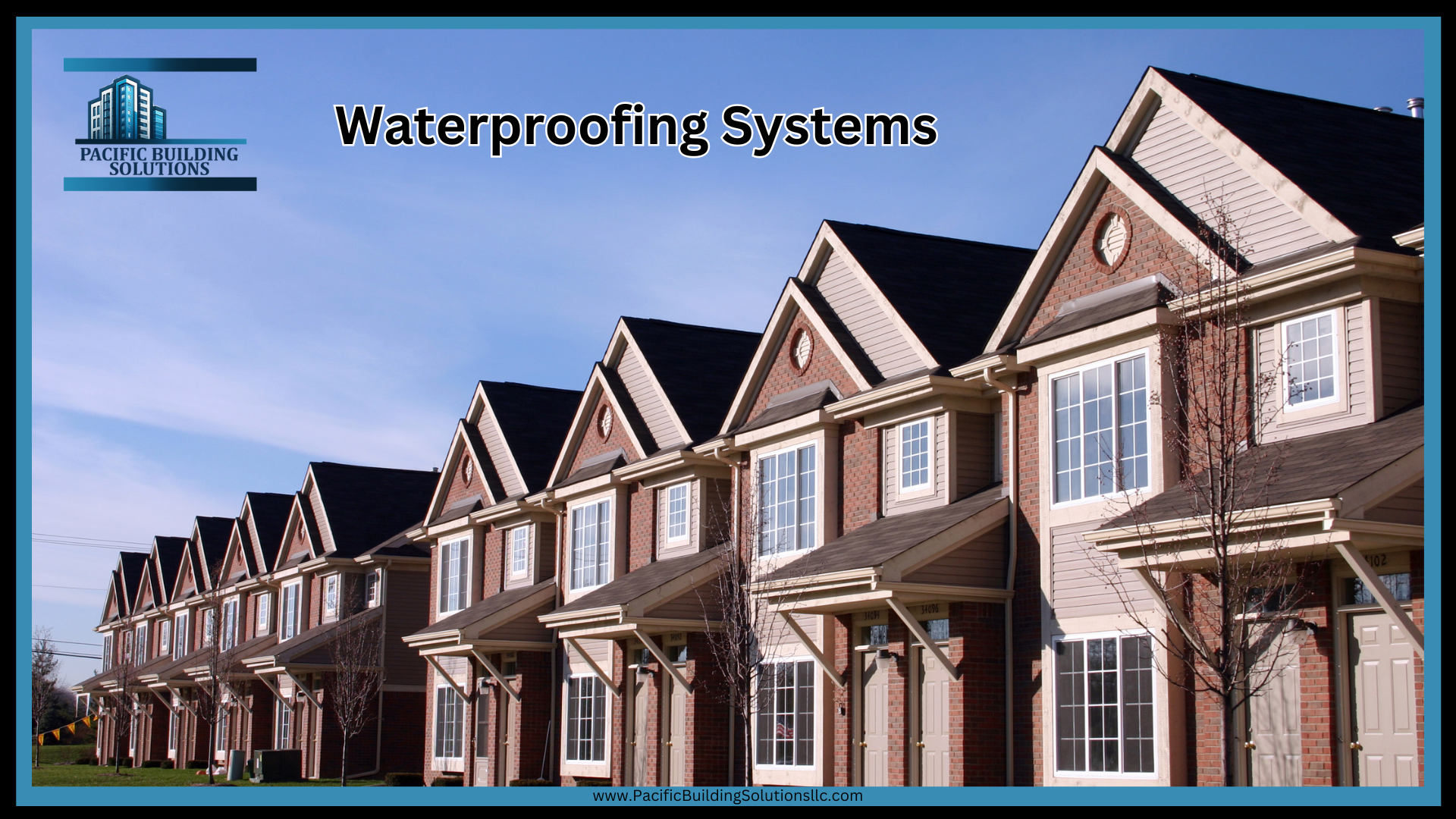
The Role of Advanced Waterproofing
When it comes to multi-family buildings, protection from water damage isn’t just a good idea—it’s a necessity. Water infiltration can weaken structures, promote mold growth, and lead to costly and time-consuming repairs. To combat these issues, utilizing the most advanced waterproofing systems is key.
At Pacific Building Solutions, LLC, we specialize in cutting-edge waterproofing technologies tailored to the specific challenges of multi-family structures. In this comprehensive guide, we’ll break down the top systems, explaining their benefits and when to use them.
Why Waterproofing Systems are Critical for Multi-Family Structures
Multi-family buildings, including apartments and condominium complexes, face unique challenges. High-density living results in more stress on the building’s infrastructure, and greater exposure to weather elements compounds these risks.
Potential Dangers of Water Intrusion:
- Structural Deterioration: Water can erode both steel and concrete over time, weakening a building’s integrity.
- Tenant Health Hazards: Mold growth in damp areas poses significant respiratory risks.
- Rising Costs: Reactive fixes are exponentially more expensive than proactive waterproofing.
You may find it surprising, but statistics show that up to 90% of building envelope failures are due to improper waterproofing. That’s a jaw-dropping number that underscores the need for effective solutions.
1. Fluid-Applied Waterproofing Membranes
Fluid-applied membrane systems are a state-of-the-art approach to waterproofing that delivers unmatched versatility and protection for multi-family buildings. Unlike traditional sheet-based solutions, these membranes are applied in a liquid form and cured into a seamless, flexible, and highly durable waterproof barrier. This method ensures a watertight seal over complex or irregular surfaces, making it a top choice for modern architectural designs.
What Are Fluid-Applied Membranes?
Fluid-applied membranes are created from advanced waterproofing materials like polyurethane, acrylic, or modified bitumen. These substances are spread or sprayed onto the desired surface, where they cure to form a continuous and impermeable layer. Because the membrane starts as a liquid, it can flow into cracks, crevices, and other hard-to-reach areas, providing comprehensive coverage and protection.
There are two main categories of fluid-applied membranes:
- Single-Component Systems: These are pre-mixed solutions, ideal for projects requiring easy application and quick turnaround times.
- Two-Component Systems: These involve mixing two separate components (a base resin and a curing agent) before application. They offer enhanced durability and are better suited for areas subject to intense water pressure or heavy traffic.
Key Benefits of Fluid-Applied Membranes
Fluid-applied membranes offer several distinct advantages over other waterproofing methods. Here’s why they’ve become a preferred choice for multi-family building projects:
- Seamless and Continuous Protection: One of the most significant benefits of fluid-applied membranes is their seamless application. Traditional waterproofing methods, like sheet membranes, have seams that can become weak points over time, leading to leaks. There are no seams or joints with fluid-applied systems—just one uniform barrier that eliminates water entry points.
- Flexibility and Movement Accommodation: Buildings naturally move and shift over time due to thermal expansion, settling, or seismic activity. Fluid-applied membranes are designed to remain flexible and stretch with the building’s movements, preventing cracking or tearing. This flexibility makes them ideal for applications in areas prone to temperature fluctuations or minor ground shifts.
- Custom Fit for Complex Designs: Many modern multi-family buildings feature intricate architectural details, such as curved walls, sharp angles, or penetrations like pipes and vents. Fluid-applied membranes conform effortlessly to these irregular shapes, covering every surface without gaps or overlaps.
- Strong Adhesion: These membranes bond tightly to various surfaces, including concrete, wood, metal, and masonry. The strong adhesion prevents water from sneaking between the membrane and the structure, reducing the risk of leaks.
- Fast and Efficient Application: A fluid membrane is generally quicker than installing traditional waterproofing sheets. While the curing time varies depending on the material and weather conditions, the streamlined process often means shorter project timelines and lower labor costs.
Best Applications for Fluid-Applied Membranes
Fluid-applied membrane systems are highly adaptable and can be used in various areas of multi-family buildings. Here’s where they work best:
- Rooftop Terraces and Balconies: These outdoor spaces are constantly exposed to rain, UV rays, and foot traffic. A fluid-applied membrane provides long-lasting protection against moisture infiltration while also enduring daily wear and temperature changes.
- Parking Decks and Podium Slabs: Multi-family buildings with parking structures or podium decks require heavy-duty waterproofing to handle vehicular traffic and exposure to the elements. Fluid-applied membranes form a resilient, slip-resistant surface that prevents water from penetrating and causing structural damage.
- Basement and Foundation Walls are particularly vulnerable to water pressure from the surrounding soil. Fluid-applied membranes seal every crack and gap, keeping basements dry even in regions with high groundwater levels.
- Complex Facades and Architectural Features: Many buildings have unique exterior designs with intricate details that are challenging to waterproof using traditional methods. Fluid-applied systems adapt perfectly to these features, providing complete coverage and eliminating the risk of weak spots.
The Application Process
Applying a fluid-applied membrane requires a meticulous approach to ensure long-lasting protection. Here’s how Pacific Building Solutions, LLC handles the process:
- Surface Preparation: The surface must be thoroughly cleaned and prepped before applying the membrane. This step includes removing dirt, oil, and previous coatings to strengthen bonds. In some cases, a primer may be applied to enhance adhesion.
- Crack and Joint Sealing: Any existing cracks or joints in the substrate are sealed with a compatible sealant. This step provides an additional layer of defense against water intrusion.
- Membrane Application: The fluid membrane is applied using a roller, brush, or specialized spray equipment. Spraying is often the most efficient method for large or high-traffic areas. The membrane is typically applied in multiple coats to achieve the desired thickness and durability.
- Curing Time: After application, the membrane needs time to cure. The curing duration depends on the material, ambient temperature, and humidity levels. Some membranes cure within hours, while others may take several days to reach full strength.
- Final Inspection: Once the membrane has cured, our team conducts a thorough inspection to ensure the coverage is even and there are no weak spots. Quality assurance is crucial to ensure the membrane will perform as expected.
Why Pacific Building Solutions, LLC Trusts Fluid-Applied Membranes
At Pacific Building Solutions, LLC, we have extensive experience using fluid-applied membrane systems for various challenging projects. We’ve successfully employed these membranes, from rooftop decks with complex drainage systems to below-grade foundation walls in flood-prone areas.
We trust fluid-applied membranes because they provide our clients with a flexible and durable waterproofing solution. These systems’ adaptability makes them a perfect match for the unpredictable climate and diverse architectural styles often found in multi-family buildings.
A Surprising Fact!
Here’s a fun fact: Fluid-applied membrane technology was originally developed for use in extreme environments, like oil rigs and industrial tanks. The technology’s ability to withstand harsh conditions and significant pressure has since made it a top choice for modern construction, ensuring long-lasting protection in even the most challenging environments.
2. Bentonite Clay Liners
Bentonite clay is a naturally occurring, absorbent material that swells when exposed to water, forming a dense, watertight seal. It’s highly effective for underground applications where constant soil moisture is challenging.
Applications:
- Below-Ground Foundations: Keeps basements dry, even in high-water-table areas.
- Slurry Walls and Landfills: A proven solution in construction and environmental projects.
Why It’s a Winner:
- Natural and Eco-Friendly: Perfect for projects that prioritize sustainability.
- Self-Sealing Properties: Automatically fills small gaps, making it maintenance-friendly.
Did you know that bentonite clay has been used since ancient times as a natural detoxifying agent in health and wellness practices? Its moisture-absorbing capabilities are legendary!
3. Pre-Fabricated Sheet Membranes
Pre-fabricated sheet membranes come as ready-to-install rolls, usually made of durable materials like rubberized asphalt or HDPE. These are perfect for large areas that need consistent waterproofing coverage.
Common Uses:
- Underground Walls and Tunnels: Protects against high-pressure water environments.
- Podium Slabs and Roof Gardens: No water seeps through to living spaces below.
Pros and Cons:
- Pros: Speedy installation and uniform thickness for dependable results.
- Cons: Seams need to be sealed carefully to maintain the barrier.
At Pacific Building Solutions, LLC, we leverage these sheets for projects requiring uniformity and where time efficiency is critical.
4. Cementitious Waterproof Coatings
Cementitious coatings are made from a cement-based compound that bonds to concrete, creating a waterproof layer. These coatings are particularly useful for water-exposed surfaces.
Where They’re Effective:
- Water Treatment Facilities: Long-lasting protection in a water-saturated environment.
- Basement and Foundation Walls: Keeps water out in heavy rain or flooding conditions.
Advantages:
- Strong Adhesion: Sticks well to masonry, making it a reliable choice for older structures.
- Easy to Apply: Requires minimal skill, reducing installation costs.
However, while durable, cementitious systems may need supplementary waterproofing in high-movement areas.
5. Elastomeric Protective Coatings
Elastomeric coatings form a durable, elastic film on exterior surfaces. Their unique property of stretching and contracting makes them perfect for walls that experience slight shifts or vibrations.
Applications:
- Exterior Facades: Offers protection from weather and helps prevent cracking.
- Roof Coatings: Seals small leaks and shields the roof from UV rays.
Perks:
- Highly Flexible: Prevents cracking over time, even in freeze-thaw cycles.
- Waterproof and Breathable: Keeps moisture out while allowing trapped water to escape.
Pacific Building Solutions, LLC utilizes elastomeric coatings on older or vulnerable facades, extending their life and appearance.
6. Interior (Negative-Side) Waterproofing
When external waterproofing isn’t possible, negative-side systems are the solution. These are applied inside the structure, blocking water from entering.
Practical Uses:
- Basement Retrofits: Ideal for older buildings with limited exterior access.
- Tunnels and Mines: Essential for infrastructure projects where excavation isn’t an option.
Why It’s Beneficial:
- Cost-Effective: This avoids the need for expensive exterior excavation.
- Multi-Purpose: Works well even under significant water pressure.
Negative-side waterproofing has been a game-changer in preserving centuries-old cathedrals, keeping their interiors dry even in humid European climates.
7. Integral Concrete Admixtures
These are chemical additives mixed directly into the concrete to make it intrinsically water-resistant. They work by blocking capillary pores and reducing water permeability.
Best for:
- New Builds: Protects foundations and walls from day one.
- Coastal Structures: Essential for buildings exposed to saltwater corrosion.
Top Benefits:
- Zero Maintenance: Protection lasts as long as the concrete does.
- Deep Sealing Power: Guards against water even if the exterior surface is damaged.
Pacific Building Solutions, LLC often suggests this robust, all-in-one protection for multi-family housing projects near water sources.
8. Hot-Applied Asphalt Systems
Hot-applied rubberized asphalt is heated until liquid, then poured onto surfaces to create a seamless and highly durable barrier. It’s often reinforced with a fabric layer for added strength.
Ideal Situations:
- Parking Structures: Endures the weight of vehicles and seasonal shifts.
- Plaza Decks: Suitable for outdoor spaces exposed to both water and heavy foot traffic.
Key Attributes:
- Long-Lasting Performance: Handles everything from extreme heat to heavy snow.
- Uniform Seal: Adheres fully to the substrate, leaving no room for leaks.
9. Cold-Applied Waterproofing Options
Cold-applied waterproofing involves spreading liquid waterproofing agents at room temperature. It’s a convenient and safe choice, especially for heat-sensitive environments.
Where It Shines:
- Occupied Spaces: Reduces disruption, as it doesn’t emit strong odors.
- Fast-Track Projects: Perfect for buildings under tight timelines.
Advantages:
- Low Volatile Organic Compounds (VOCs): Eco-friendly and tenant-friendly.
- Quick Curing: Sets faster than traditional methods.
Pacific Building Solutions, LLC often deploys these products in settings where time and comfort are of the essence.
10. Self-Stick Waterproof Membranes
Self-adhering membranes simplify the waterproofing process. These peel-and-stick sheets create a strong bond with various substrates, making them effective and easy to install.
Uses:
- Foundation Protection: Seals around basement walls, preventing leaks.
- Flashing Details: Ideal for windows and doors where water ingress is common.
Perks:
- Ease of Application: Minimal tools required.
- Reliable Adhesion: Works even in cooler climates.
11. High-Performance Drainage Mats
High-performance drainage mats are an essential, often overlooked, component of a comprehensive waterproofing system for multi-family buildings. These mats are engineered to manage and direct water away from the building’s foundation, protecting it from the damaging effects of hydrostatic pressure and seepage.
What Are Drainage Mats?
Drainage mats, boards, and composite drainage systems are typically made of a high-density polyethylene (HDPE) core. This core is designed with a series of dimples or grooves that create air gaps, allowing water to flow freely through channels. The mats are often paired with a non-woven geotextile fabric, which filters soil particles while allowing water to pass through. The result is a highly effective drainage system that keeps water from accumulating against the building’s foundation.
How They Work
When installed, drainage mats create a space between the foundation wall and the surrounding soil. This space allows any water that seeps through the soil to flow down the mat and away from the foundation. By relieving hydrostatic pressure, drainage mats help to ensure that water doesn’t force its way into the structure, reducing the risk of leaks, moisture intrusion, and subsequent water damage.
Key Features
- Efficient Water Flow: The dimpled structure channels water downward efficiently, even in areas with heavy rainfall or high water tables.
- Soil Filtration: The geotextile fabric layer prevents soil and debris from clogging the drainage channels, ensuring long-term functionality.
- Durable Materials: Made from tough, rot-resistant plastics, drainage mats are built to withstand extreme temperatures, soil pressure, and chemical exposure.
Where to Use High-Performance Drainage Mats
Drainage mats are versatile and can be used in various parts of a multi-family building’s waterproofing strategy. Here’s where they are most effective:
- Below-Grade Foundation Walls: One of the most common uses for drainage mats is around a building’s foundation, especially in basements or underground garages. They prevent water from pooling against the foundation, reducing the risk of seepage and structural damage.
- Living (Green) Roofs: Drainage mats are installed beneath the soil layer on green roofs to manage excess water. They ensure that plant roots do not become waterlogged and that the building’s roof membrane is protected from constant moisture.
- Retaining Walls: Retaining walls are designed to hold back soil but often under significant pressure from water buildup. Installing drainage mats ensures water is directed away from the wall, protecting its structural integrity and preventing erosion.
Why Drainage Mats Are Critical for Multi-Family Buildings
In multi-family buildings, where structural issues can quickly multiply and affect numerous residents, the role of drainage mats becomes even more crucial. Here’s why:
- Preventing Moisture-Related Problems: Drainage mats direct water away from the foundation, minimizing the risk of moisture-related issues such as mold growth, interior water damage, and structural weakening.
- Protecting Structural Integrity: When water pressure builds up around the foundation, it can lead to cracks and even foundation failure. Drainage mats help relieve this pressure, keeping the structure stable and sound.
- Reducing Maintenance Costs: Drainage mats prevent water damage, reducing the need for costly repairs and interventions in the future. They are a proactive solution that pays off in the long term.
Installation Considerations
- Proper Placement: For maximum effectiveness, drainage mats should be installed by professionals with expertise in below-grade waterproofing. The mats must be properly secured to the foundation wall, and the drainage system should be correctly graded to channel water away from the building.
- Integration with Other Waterproofing Systems: Drainage mats are often combined with other waterproofing techniques, such as sheet membranes or bentonite clay barriers, to provide comprehensive protection. The entire system should be designed to work together, ensuring that water is directed away from the building and does not collect in unwanted areas.
Real-World Example from Pacific Building Solutions, LLC
At Pacific Building Solutions, LLC, we’ve implemented high-performance drainage mats in various challenging projects. For example, in a recent multi-family development built on a sloping lot, drainage mats were key to managing the substantial runoff that flowed toward the building’s foundation. By incorporating these mats into the waterproofing strategy, we ensured that the property remained dry and stable, even during the heaviest storms.
You might be surprised to learn that ancient water management systems inspire the idea behind modern drainage mats. The Inca civilization, for example, designed agricultural terraces with built-in drainage channels to prevent landslides and manage rainfall effectively. Today’s drainage mats serve a similar purpose, keeping our structures safe and dry using centuries-old principles of water flow.
Conclusion
Choosing the right waterproofing method for your multi-family building is an investment in long-term durability and tenant satisfaction. At Pacific Building Solutions, LLC, we take pride in offering customized solutions that protect your assets and give you peace of mind.
FAQs for Waterproofing Systems
What’s the best waterproofing method for large-scale multi-family buildings?
It depends on the building’s specific needs. Fluid-applied membranes and integral additives are versatile, but a professional assessment is essential.
How often should waterproofing solutions be inspected?
Annual inspections are recommended to catch any potential failures before they escalate into costly repairs.
Can combining multiple waterproofing methods increase protection?
Yes! Combinations like drainage mats with sheet membranes provide a comprehensive moisture defense system.
Ready to future-proof your property? Contact Pacific Building Solutions, LLC for expert advice and to learn which waterproofing solutions work best for your building’s needs.
Oregon Zip Codes Served:
Multnomah County
97019 (Corbett)
97024 (Fairview)
97030 (Gresham)
97080 (Gresham)
97201 (Portland)
97202 (Portland)
97203 (Portland)
97204 (Portland)
97205 (Portland)
Washington County
97006 (Aloha)
97007 (Aloha)
97106 (Banks)
97008 (Beaverton)
97005 (Beaverton)
97229 (Bethany)
97109 (Buxton)
97113 (Cornelius)
97116 (Forest Grove)
97117 (Gales Creek)
97119 (Gaston)
97123 (Hillsboro)
97124 (Hillsboro)
97125 (Manning)
97133 (North Plains)
97140 (Sherwood)
97223 (Tigard)
97224 (Tigard)
97144 (Timber)
97062 (Tualatin)
97225 (West Haven-Sylvan)
Clackamas County
97004 (Beavercreek)
97009 (Boring)
97013 (Canby)
97015 (Clackamas)
97017 (Colton)
97089 (Damascus)
97022 (Eagle Creek)
97023 (Estacada)
97027 (Gladstone)
97028 (Government Camp)
97086 (Happy Valley)
97034 (Lake Oswego)
97035 (Lake Oswego)
97222 (Milwaukie)
97038 (Molalla)
97067 (Mount Hood Village)
97011 (Mount Hood Village)
97049 (Mount Hood Village)
97042 (Mulino)
97267 (Oak Grove)
97045 (Oregon City)
97055 (Sandy)
97068 (West Linn)
97070 (Wilsonville)
Marion County
97325 (Aumsville)
97002 (Aurora)
97342 (Detroit)
97020 (Donald)
97317 (Four Corners)
97346 (Gates)
97026 (Gervais)
97305 (Hayesville)
97032 (Hubbard)
97350 (Idanha)
97352 (Jefferson)
97303 (Keizer)
97384 (Mehama)
97362 (Mount Angel)
97373 (Saint Benedict)
97137 (Saint Paul)
97301 (Salem)
97302 (Salem)
97306 (Salem)
97375 (Scotts Mills)
97381 (Silverton)
97383 (Stayton)
97385 (Sublimity)
97392 (Turner)
97071 (Woodburn)
Columbia County
97016 (Clatskanie)
97018 (Columbia City)
97054 (Deer Island)
97048 (Rainier)
97056 (Scappoose)
97051 (St. Helens)
97064 (Vernonia)
97053 (Warren)
Yamhill County
97101 (Amity)
97111 (Carlton)
97114 (Dayton)
97115 (Dundee)
97127 (Lafayette)
97128 (McMinnville)
97132 (Newberg)
97378 (Sheridan)
97396 (Willamina)
97148 (Yamhill)